Аммиак — один из самых распространённых химических продуктов, производимых в промышленности, уступающий по объёмам лишь серной кислоте. Рынок растёт примерно на 1,4% в год, при общемировом производстве около 140 млн тонн. Производство аммиака из азота и водорода включает два основных этапа: во-первых, получение водорода, а во-вторых — синтез аммиака (процесс Габера). Водородные установки требуют непрерывной и надёжной работы оборудования для оптимизации производства и снижения энергозатрат. Многие предприятия вынуждены снижать температуру, жертвуя производительностью. Однако исследования показали, что снижение температуры всего на 10°C приводит к снижению производительности на 1%. Задача водородных установок — поддержание точной температуры для максимальной эффективности при одновременном обеспечении непрерывной работы оборудования.
Паровой риформинг природного газа — один из наиболее распространённых термических методов получения водорода. Растущий мировой спрос на водород способствует расширению применения таких риформеров, при этом на первый план выходят требования к максимальной производительности. В то же время возрастает интерес к инспекции и диагностике в производстве водорода, метана и аммиака. Это связано с необходимостью повышения безопасности, сокращения простоев и снижения затрат.
В ходе процесса природный газ реагирует с водяным паром в присутствии катализатора при высоких температурах (700–1000°C) под давлением. Результатом реакции являются оксид углерода, водород и небольшое количество CO₂. На следующем этапе оксид углерода взаимодействует с паром с образованием дополнительного водорода. Затем удаляется CO₂, и остаётся чистый водород. Весь процесс сопровождается теплопередачей от сжигания газа в печи к каталитическим трубкам.
Риформеры, применяемые в производстве аммиака, водорода и метанола, представляют собой сложные, энергоёмкие и дорогие установки. Мониторинг температуры стенки труб (TMT) помогает продлить срок службы труб, повысить энергоэффективность и производительность. Трубы располагаются в виде параллельных рядов между горелками, размещёнными либо сверху, либо снизу печи, температура в печи может достигать 1000–1100°C. В других конфигурациях трубы могут размещаться между противоположными стенками печи. Реакция происходит в трубах при температуре около 900°C, выход — снизу.
Паровой риформинг природного газа — один из наиболее распространённых термических методов получения водорода. Растущий мировой спрос на водород способствует расширению применения таких риформеров, при этом на первый план выходят требования к максимальной производительности. В то же время возрастает интерес к инспекции и диагностике в производстве водорода, метана и аммиака. Это связано с необходимостью повышения безопасности, сокращения простоев и снижения затрат.
В ходе процесса природный газ реагирует с водяным паром в присутствии катализатора при высоких температурах (700–1000°C) под давлением. Результатом реакции являются оксид углерода, водород и небольшое количество CO₂. На следующем этапе оксид углерода взаимодействует с паром с образованием дополнительного водорода. Затем удаляется CO₂, и остаётся чистый водород. Весь процесс сопровождается теплопередачей от сжигания газа в печи к каталитическим трубкам.
Риформеры, применяемые в производстве аммиака, водорода и метанола, представляют собой сложные, энергоёмкие и дорогие установки. Мониторинг температуры стенки труб (TMT) помогает продлить срок службы труб, повысить энергоэффективность и производительность. Трубы располагаются в виде параллельных рядов между горелками, размещёнными либо сверху, либо снизу печи, температура в печи может достигать 1000–1100°C. В других конфигурациях трубы могут размещаться между противоположными стенками печи. Реакция происходит в трубах при температуре около 900°C, выход — снизу.
Проблемы эксплуатации
Основные проблемы управления и контроля TMT связаны с горелками, распределением дымовых газов и катализатором. Все эти факторы могут вызвать преждевременный выход труб из строя. Чтобы этого избежать, операторы часто работают с заниженными температурами, теряя производительность. Даже в этом случае перегрев может возникнуть из-за локальных "горячих точек". Повреждение труб и нарушения потока процесса при перегреве могут привести к серьёзным убыткам. Всего +20°C к расчетной температуре может сократить срок службы трубы вдвое. Поэтому непрерывный мониторинг температуры крайне важен.
Температура на внешней поверхности трубы может достигать 960°C, внутри — от 450 до 900°C. Проблемы могут быть в виде ползучести, термическом растрескивании, разрушении структуры и перегрева. Особенно значим температурный градиент в нижней части трубы, вызывающий дифференцированную деформацию (ползучесть) — одну из основных причин разрушения. До 20% аварий приходится на растрескивание труб. Но основная причина катастрофических сбоев — человеческий фактор.
Операторы должны глубоко понимать поведение реформера: анализировать данные и быстро принимать решения. Также важны знания в области теплообмена, радиационного фона, эмиссионной способности и влияния охлаждения при открывании смотрового окна. Регулярное открытие таких окон может снизить температуру труб в зоне обзора до 30°C. Поэтому данные TMT должны быть точными, воспроизводимыми и надёжными. С возрастом трубы прогреваются неравномерно, и новые трубы будут вести себя иначе, чем старые — балансировка становится затруднённой. Для эффективного управления активами необходим точный контроль температуры в режиме реального времени.
Методы измерения температуры
Для обеспечения производительности, безопасности и энергоэффективности требуется непрерывный мониторинг. Наиболее эффективные методы:
Основные проблемы управления и контроля TMT связаны с горелками, распределением дымовых газов и катализатором. Все эти факторы могут вызвать преждевременный выход труб из строя. Чтобы этого избежать, операторы часто работают с заниженными температурами, теряя производительность. Даже в этом случае перегрев может возникнуть из-за локальных "горячих точек". Повреждение труб и нарушения потока процесса при перегреве могут привести к серьёзным убыткам. Всего +20°C к расчетной температуре может сократить срок службы трубы вдвое. Поэтому непрерывный мониторинг температуры крайне важен.
Температура на внешней поверхности трубы может достигать 960°C, внутри — от 450 до 900°C. Проблемы могут быть в виде ползучести, термическом растрескивании, разрушении структуры и перегрева. Особенно значим температурный градиент в нижней части трубы, вызывающий дифференцированную деформацию (ползучесть) — одну из основных причин разрушения. До 20% аварий приходится на растрескивание труб. Но основная причина катастрофических сбоев — человеческий фактор.
Операторы должны глубоко понимать поведение реформера: анализировать данные и быстро принимать решения. Также важны знания в области теплообмена, радиационного фона, эмиссионной способности и влияния охлаждения при открывании смотрового окна. Регулярное открытие таких окон может снизить температуру труб в зоне обзора до 30°C. Поэтому данные TMT должны быть точными, воспроизводимыми и надёжными. С возрастом трубы прогреваются неравномерно, и новые трубы будут вести себя иначе, чем старые — балансировка становится затруднённой. Для эффективного управления активами необходим точный контроль температуры в режиме реального времени.
Методы измерения температуры
Для обеспечения производительности, безопасности и энергоэффективности требуется непрерывный мониторинг. Наиболее эффективные методы:
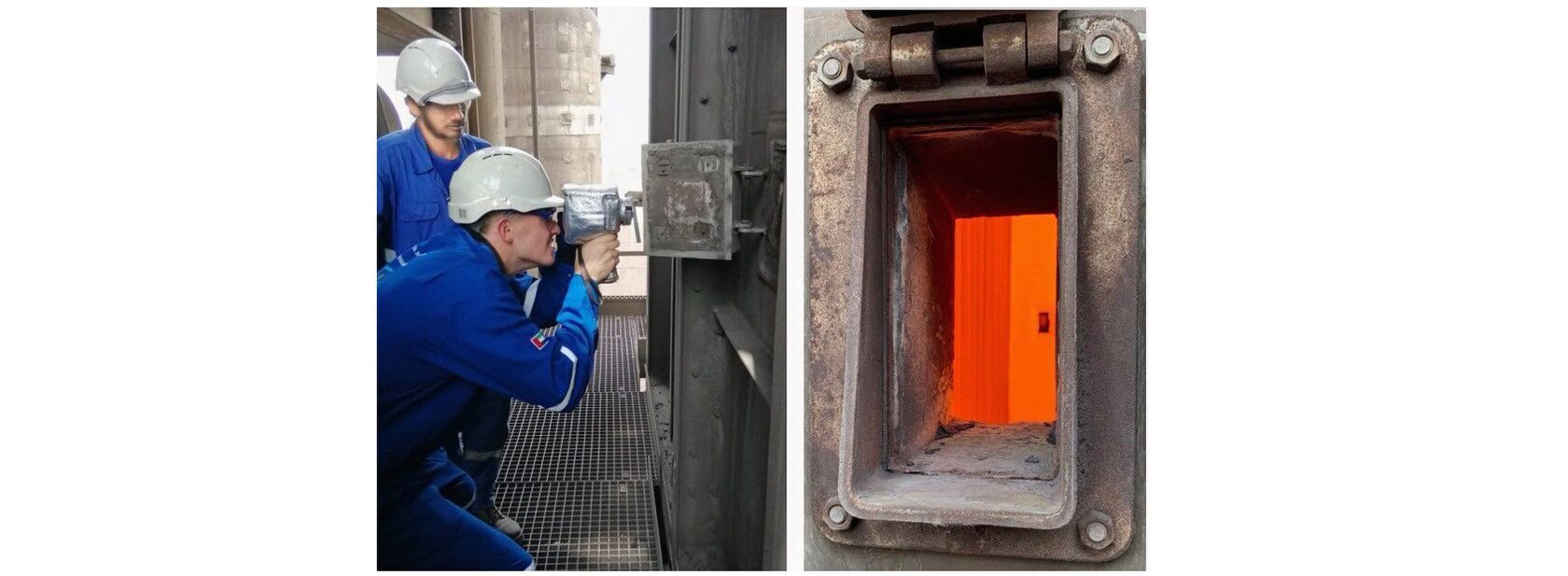
Портативные пирометры — позволяют проводить точечные измерения. Высокоточные, признаны отраслевым стандартом. Помогают удерживать режим близко к проектному. Однако охватывают только одну точку и могут пропустить "горячие зоны".
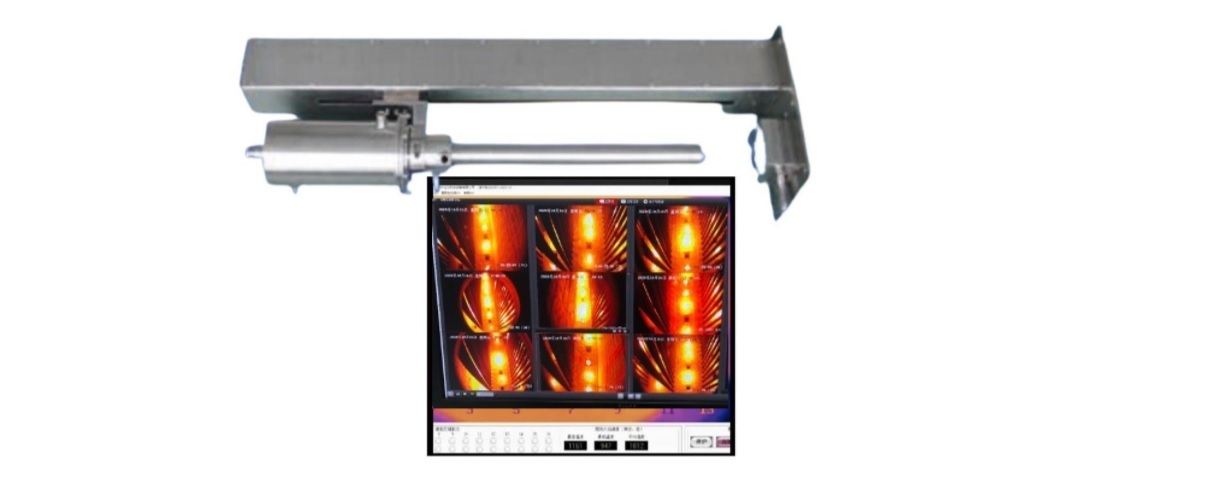
Фиксированные тепловизионные камеры — обеспечивают более точные и воспроизводимые данные, не зависят от человеческого фактора. Камеры устанавливаются внутрь реформера и проводят непрерывные постоянные измерения температуры. Охлаждаются водой или воздухом, что позволяет камере находится в работе 24/7. Этот метод минимизирует риск аварий и повышает эффективность.
Стационарные инфракрасные тепловизоры
Точные измерения требуют учёта излучательной способности измеряемых объектов.. Внутри реформера множество отражающих объектов, что может ввести в заблуждение при визуальной оценке или пирометрии. Тепловизоры монтируются стационарно, производится настройка излучательной способности для всей ключевых видимых областей, что приводит к избеганию таких ошибок.
Камера даёт изображение высокой чёткости с реальными показаниями температуры по всей видимой поверхности трубы и огнеупоров. Горизонтальное поле зрения 90° позволяет одновременно контролировать несколько труб. Это повышает безопасность, эффективность и управляемость печи.
Точные измерения требуют учёта излучательной способности измеряемых объектов.. Внутри реформера множество отражающих объектов, что может ввести в заблуждение при визуальной оценке или пирометрии. Тепловизоры монтируются стационарно, производится настройка излучательной способности для всей ключевых видимых областей, что приводит к избеганию таких ошибок.
Камера даёт изображение высокой чёткости с реальными показаниями температуры по всей видимой поверхности трубы и огнеупоров. Горизонтальное поле зрения 90° позволяет одновременно контролировать несколько труб. Это повышает безопасность, эффективность и управляемость печи.
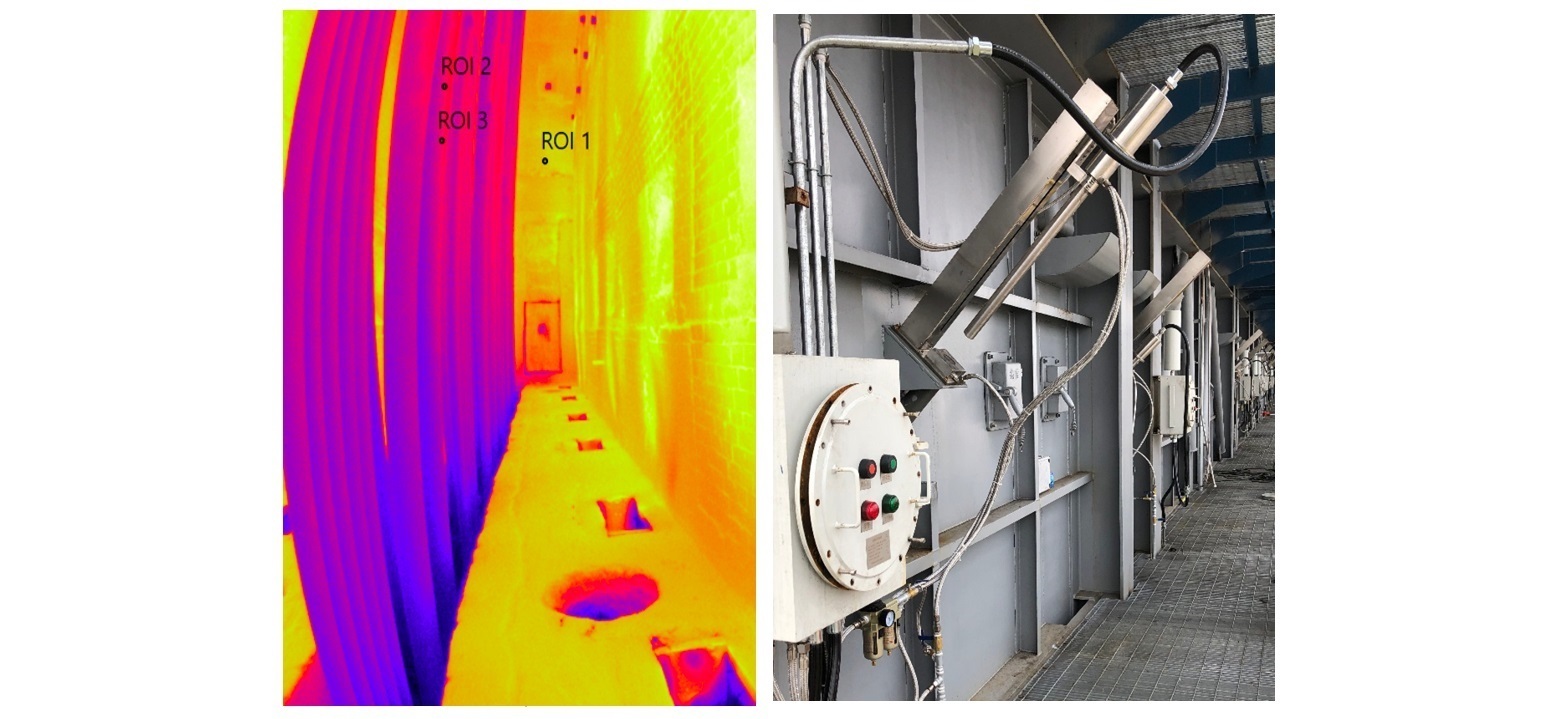
Тепловизионная камера позволяет в реальном времени видеть распределение температур, выявлять зоны перегрева, неисправные горелки, работу и влияние факела. Коротковолновой рабочий спектр камеры сводит к минимуму ошибки от различной эмиссионной способности. Данные можно архивировать и анализировать на протяжении всего срока службы оборудования.
Использование тепловизионных камер даёт возможность контролировать температуру не только во время работы, но и на этапах запуска и остановки, оптимизируя энергорасход. Специализированное ПО может выдавать сигналы тревоги при достижении критической температуры, позволяя оператору своевременно реагировать. Также можно формировать тренды TMT, проводить оценку остаточного ресурса труб, планировать замену, интегрировать систему в АСУ ТП и просматривать события до срабатывания сигнализации.
Некоторые производители водорода уже отмечают повышение производительности на 2% при сохранении безопасного режима, благодаря такому тепловизионному инфракрасному мониторингу.
Вывод
Растущий спрос на аммиак требует повышения производительности, безопасности и снижения затрат. Постоянный температурный мониторинг с помощью стационарных инфракрасных тепловизионных камер становится ключом к решению этих задач.
Управление активами невозможно без надёжного измерения температуры. Перегрев приводит к резкому снижению срока службы оборудования. Правильное управление температурой при запуске, работе и остановке продлевает ресурс труб и катализатора, снижает простои и уменьшает количество внеплановых остановок.
Фиксированное тепловизионное измерение — это важный шаг вперёд для промышленной газовой отрасли. Использование решений инфракрасного мониторинга способствует росту производительности, надёжности и безопасности, сокращает необходимость нахождения персонала в опасных зонах. Круглосуточный мониторинг позволяет эксплуатировать установку ближе к проектным пределам без риска.
В условиях высокой сложности парового реформинга, стационарные инфракрасные тепловизоры дают операторам необходимые инструменты для принятия обоснованных решений, оптимизации процессов и повышения эффективности производства.
Использование тепловизионных камер даёт возможность контролировать температуру не только во время работы, но и на этапах запуска и остановки, оптимизируя энергорасход. Специализированное ПО может выдавать сигналы тревоги при достижении критической температуры, позволяя оператору своевременно реагировать. Также можно формировать тренды TMT, проводить оценку остаточного ресурса труб, планировать замену, интегрировать систему в АСУ ТП и просматривать события до срабатывания сигнализации.
Некоторые производители водорода уже отмечают повышение производительности на 2% при сохранении безопасного режима, благодаря такому тепловизионному инфракрасному мониторингу.
Вывод
Растущий спрос на аммиак требует повышения производительности, безопасности и снижения затрат. Постоянный температурный мониторинг с помощью стационарных инфракрасных тепловизионных камер становится ключом к решению этих задач.
Управление активами невозможно без надёжного измерения температуры. Перегрев приводит к резкому снижению срока службы оборудования. Правильное управление температурой при запуске, работе и остановке продлевает ресурс труб и катализатора, снижает простои и уменьшает количество внеплановых остановок.
Фиксированное тепловизионное измерение — это важный шаг вперёд для промышленной газовой отрасли. Использование решений инфракрасного мониторинга способствует росту производительности, надёжности и безопасности, сокращает необходимость нахождения персонала в опасных зонах. Круглосуточный мониторинг позволяет эксплуатировать установку ближе к проектным пределам без риска.
В условиях высокой сложности парового реформинга, стационарные инфракрасные тепловизоры дают операторам необходимые инструменты для принятия обоснованных решений, оптимизации процессов и повышения эффективности производства.
29.05.2025